|
|
 |
 |
|
 |
|
Plenary Lectures |
Plenary Lecture 1:Overview of research activities on the synthesis and characterization of particle reinforced Al and W-based composites
Time: 13th of APRIL, 2015, 09:10-09:40
Invited Speaker: Prof. Dr. Lutfi Ovecoglu ( Istanbul Technical University, Turkey)
Biography:
M. Lütfi Öveçoğlu is Professor in the department of Metallurgical and Materials Engineering at Istanbul Technical University. He received his M. S. and Ph. D. degrees in Materials Science and Engineering from Stanford University in Stanford, CA, U. S. A. in 1987. He worked at Xerox PARC for one year and as Technical Manager at Devtech B. V. in the Netherlands for two years following his Ph. D. He became faculty member in the department of Metallurgical and Materials Engineering of Istanbul Technical University in 1990 and has since been in this position. He is the founder and technical director of a cluster of 9 laboratories named Particulate Materials Laboratories (PML). He was awarded the TÜBİTAK Encouragement Award (Teşvik Ödülü) in Engineering in 1997 and the Turkish Ceramic Federation Ceramic Honorary Award in 2010. He is author or co-author of 145 papers cited in Web of Science, 2 book chapters and 3 edited conference proceedings with about 949 citations to his work which mostly related to metal matrix composites (MMCs) and ceramic matrix composites (CMCs). PML group consists of 3 professors, 1 associated professor, 3 doctorate researchers, 15 PhD candidates and 16 graduate students.
Abstract:
Metal matrix composites (MMCs) reinforced with discontinuous phases in the forms of short fibers, whiskers, and particulates exhibit considerably enhanced strength values at room temperature or at higher temperatures, low coefficient of thermal expansion, good wear resistance and stiffness compared to the corresponding unreinforced alloys. Mechanical alloying (MA) is a solid-state powder processing technique involving repeated welding, fracturing, and rewelding of powder particles in a high-energy ball mill and it is used to produce composite metal powders, metastable crystalline and quasicrystalline phases and amorphous alloys with controlled submicron sized novel microstructures and/or nanostructures. In the last three decades, mechanical alloying has been shown to be capable of mechanochemically synthesizing a variety of equilibrium and non-equilibrium alloy phases starting from blended elemental or prealloyed powders. Aluminum-based metal matrix composite synthesized via mechanical alloying (MA) which have received considerable attraction as structural materials in aerospace, automotive and transportation industries due to their high specific modulus and strength, superior wear, fatigue and creep resistances. It is generally known that the Al composites containing hard particles exhibit high wear resistance depending on volume fraction, size and type of reinforcements compared to the matrix alloy. Tungsten (W) and its composite which are candidate materials for important structural applications at high temperatures due to their excellent properties such as high melting point, high elastic modulus, high thermal shock resistance, low thermal expansion coefficient, good corrosion resistance and good high temperature strength and stiffness. There are lots of our studies about tungsten composites reinforced various oxide and borides particles to enhance high temperature strength and creep resistance of tungsten and its alloys.
Plenary Lecture 2: Dynamic failure of curved CFRP composite laminates under quasi-static loading
Time: 13th of APRIL, 2015, 13:30-14:00
Invited Speaker: Assoc. Prof. Dr. Demirkan Coker ( Middle East Technical University, Turkey)
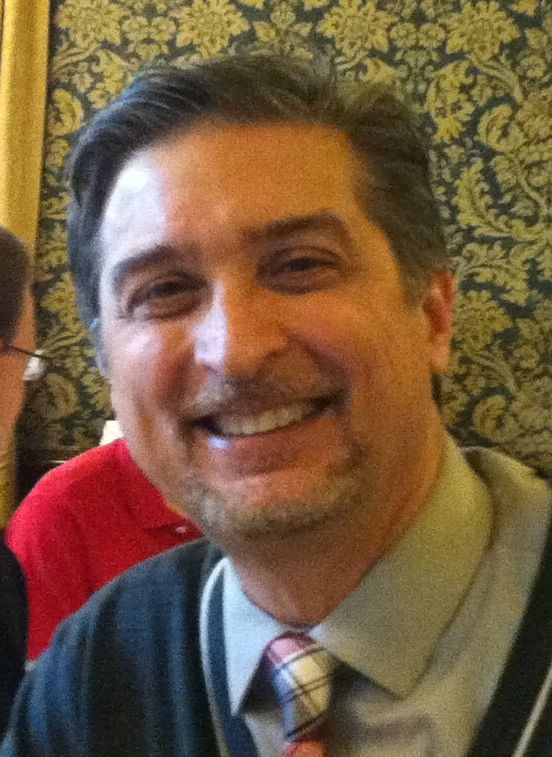
Biography:
Dr. Coker is currently Associate Professor in Aerospace Engineering and Director of Structural Mechanics and Materials Laboratory at RÜZGEM, METU. He acted as a vice-Chair of the Dept. of Aerospace Engineering from 2009-2012. Dr. Coker holds a B.S. degree in Aeronautical Engineering from METU, an M.Sc. degree in Aerospace Engineering from University of Dayton, an M.Sc. degree in Applied Mathematics from Wright State University and a Ph.D degree in Aeronautics with a minor in Geophysics from California Institute of Technology (Caltech). After Dr. Coker obtained his B.S., he started his career as a research engineer at the UDRI and at the Materials Lab/Wright Laboratories, Dayton, carrying out research on thermomechanical fatigue of novel high temperature composite materials for the hypersonic National Aerospace Plane project. During his Ph. D. studies at Caltech he carried out groundbreaking experimental work on dynamic fracture of composite materials. Afterwards he worked as a Post-Doctoral research associate at Brown University on dynamic friction modeling (2001-2004) and worked as an Assistant Professor at Oklahoma State University (2004-2008). He also worked as a visiting Professor at KITP, the University of California at Santa Barbara and EPFL in Lausanne. Dr. Coker has published 24 peer reviewed articles and 23 conference proceedings, gave more than 50 international conference talks and more than 30 invited talks in the fields of fatigue, fracture mechanics, friction, dynamic failure, experimental mechanics, computational mechanics and composite materials. In addition, he has been instrumental in setting up the undergraduate aerospace labs at METU, structure and materials labs at RUZGEM and micro-and nano-mechanics laboratory at Oklahoma State University.
Abstract:
In aerospace and wind energy industries, new advances in composite manufacturing technology and high demand for lightweight structures are fostering the use of composite laminates in a wide variety of shapes as primary load carrying elements. However, once a moderately thick laminate takes highly curved shape, such as an L-shape, Interlaminar Normal Stresses (ILNS) are induced together with typical Interlaminar Shear Stresses (ILSS) on the interfaces between the laminas. The development of ILNS promotes mode-I type of delamination propagation in the curved part of the L-shaped structure, which is a problem that has recently raised to the forefront in in-service new composite wind turbines. Delamination propagation in L-shaped laminates can be highly dynamic even though the loading is quasi-static. An experimental study to investigate dynamic delamination under quasi-static loading is carried out using a million fps high-speed camera. Simulations of the experiments are conducted with a bilinear cohesive zone model implemented in user subroutine of the commercial FEA code ABAQUS/explicit. The experiments were conducted on a 12-layered woven L-shaped CFRP laminates subjected to shear loading perpendicular to the arm of the specimen with a free-sliding fixture to match the boundary conditions used in the FEA. A single delamination is found to initiate at the 5th interface during a single drop in the load. The delamination is then observed to propagate to the arms at intersonic speed of 2200m/s. The results obtained using cohesive zone models in the numerical simulations were found to be in good agreement with experimental results in terms of load displacement behavior and delamination history. These results are the first conclusive evidence of intersonic delamination in composite materials triggered under quasistatic loading.
Plenary Lecture 3: Challenge of Nano in the Macro world of composites: Are we there yet?
Time: 14th of APRIL, 2015, 08:50-09:20
Invited Speaker: Assoc. Prof. Dr. Melih Papila ( Sabancı University, Turkey)
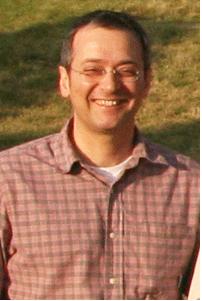
Biography:
Melih Papila received his B.S. (1990) and M.S. (1995) degrees in Aeronautical Engineering from the Middle East Technical University, Ankara, Turkey. Dr. Papila participated in a training program and worked as an engineer in structural testing department of CASA, Madrid (1992). He then worked at Roketsan, Ankara (1993 - 1997) as an R&D engineer and assumed full responsibility in a multi-national and –institutional research and technology project on high performance structural composites. He started his PhD studies (1997) and received his degree in Aerospace Engineering from the University of Florida, Gainesville (2001), as a member of Multidisciplinary and Structural Optimization group.
Dr. Papila is currently a faculty member as an Associate Professor in the Materials Science and Nanoengineering Program at Sabancı University (SU), Istanbul, Turkey. Prior to joining SU in 2004, he was a Postdoctoral Associate jointly in Interdisciplinary Microsystems and Multidisciplinary and Structural Optimization Groups at the Department of Aerospace and Mechanical Engineering of University of Florida (2002 – 2004). Dr. Papila is a recipient of EU FP7 Marie Curie International Outgoing Fellowship. He joined Composites Design Group as a visiting professor in Aeronautics & Astronautics Department at Stanford University (2010-2012).
Dr. Papila has developed expertise in design of experiments and surrogate modeling, manufacturing, testing, analysis and design of advanced composite materials and structures. His current research aims to integrate the nano-scale materials into applied macro world of composite structures, covering aspects in multiscale engineering of the high performance composites.
Abstract:
Advanced composites have become indispensible resource in a variety of fields such as aerospace, automotive and energy as they enable lighter structures without sacrificing the safety. Their full potential is yet to be met calling engineers and scientists to push the boundaries of research and development on composites for making them even more competitive and promising. In other words, we are urged to “think outside the box” practices with advancing manufacturing and characterization techniques and software specialized on composites as opposed to traditional lay-ups, materials and production. This challenge we are in is arguably dominated by the multi-scale nature of the composites. With the era of nanomaterials and their integration into macro world of composites, importance of the understanding and ability to design and manipulate the mechanisms bridging the scales, are further pronounced. Therefore, research front incorporating a multi-scale framework is essential.
Figure 1: A multi-scale framework for engineering advanced composites.
A nano-enhanced/augmented structural composite/material concept has been studied within such a multi-scale engineering framework (Fig.1), and its review is presented herein. The concept is realized by integration of the nano-scale in the form of nanofibrous interlayers into the polymer matrix composites. The nanofiber mats as interleafs may find extensive use in nearly all traditional light-weight laminated and sandwich structural applications where advanced composites are necessary. They can be easily incorporated into existing manufacturing processes and provide substantially enhanced mechanical properties, while the weight and thickness increase associated with interleaving is nearly negligible. Additionally, the possibilities for composite nanofibers by combining with particles/fillers allow the toughening performance to be further enhanced. Their full potential is even higher with multi-functional capabilities, such as tuning of mechanical, thermal and electrical properties by the right choices of nanofiber and filler combinations and proportions. With a thorough understanding of impact on the properties by the nanofibrous interlayers, the opportunities are plentiful for developing characterization and scaled-up production capabilities and integration of the nanofibrous materials into conventional composite materials and engineering design frameworks.
A road map and a series of examples are presented for effective incorporation of the electrospun nanofiber interlayers/interleafs into the laminated composites. The research hypothesis is that issues contributing to poor interlaminar strength and toughness can be delayed or eliminated by interleaving, in addition to suppressing matrix cracking, whether the root cause of delamination is isolated or synchronous. Toughening mechanisms in the presence of nanofiber interleafs are shown to be effective under both in-plane and out-of-plane loading. Specifically, epoxy-compatible poly(styrene-co-glycdylmethacrylate), P(St-co-GMA) and P(St-co-GMA)/MWCNT nanofibrous interlayers incorporated into carbon/epoxy laminated composites are exemplified for enhancing mechanical behavior (Fig.2). Tests performed are longitudinal and transverse tension, open hole tension, three point bending, end notched flexural tests, Charpy Impact and Split-Hopkinson bar test. The working mechanism of these interlayers under in-plane loads is further elaborated by the custom design tensile tests of (02/904)s interleaved laminates, backed-up by acoustic recording and analysis. Influence of the nanofibrous interleafs on the extended fatigue life of the laminates is also demonstrated.
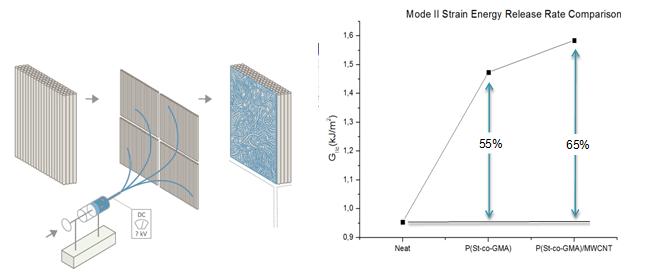
Figure 2: Representation of modified prepregs by nanofibrous interleafs and enhanced mechanical properties
Acknowledgement: TUBITAK Grant numbers 109M651, 213M542 and European Commission under the Marie Curie International Outgoing Fellowship Programme, Grant FP7-PEOPLE-2010-IOF-274737.
1. Ozden, E., Menceloğlu, Y. Z., Papila, M. "Engineering Chemistry of Electrospun Nanofibers and Interfaces in Nanocomposites for Superior Mechanical Properties,” Applied Materials&Interfaces, Vol. 2 (7), pp.1788-93, July 2010.
2. Yenigun-Ozden E., Menceloğlu, Y. Z., Papila, M., "MWCNTs/P(St-co-GMA) composite nanofibers of engineered interface chemistry for epoxy matrix nanocomposites,” Applied Materials&Interfaces, Vol. 4 (2), pp.777-784, February 2012.
3. Bilge, K., Yenigün-Özden, E., Şimşek, E., Menceloğlu, Y. Z., Papila, M., “Structural Composites Hybridized with Epoxy Compatible Polymer/MWCNT Nanofibrous Interlayers,” Composites Science and Technology, Vol. 72 (4), pp.1639-1645, July 2012.
4. Bilge, K., Venkataraman, , S., Menceloğlu, Y. Z., Papila, M., "Global and Local Nanofibrous Interlayer Toughened Composites for Higher In-Plane Strength, ” Composites Part A: Applied Science and Manufacturing, Vol. 58, pp.73-76, March 2014.
5. Bilge, K., Papila, M., “Chapter 10: Interlayer toughening mechanisms of composite materials,” in Toughening Mechanisms in Composite Materials, edited by Q. Qin, and J. Ye, Elsevier-Woodhead Publishing-Elsevier, in press, June 2015.
|
|
|
|

|
 |
|
|
|